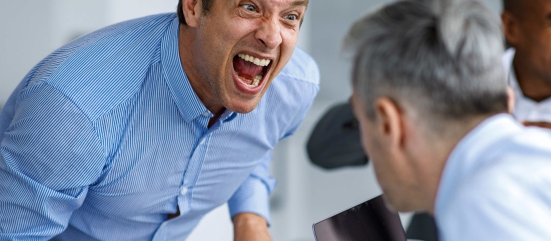
In het dagelijks leven kom je regelmatig de term ‘Lean’ of ‘Lean Management’ tegen. Hier wordt vaak hetzelfde mee bedoeld, namelijk de Lean filosofie die jaren geleden bij Toyota werd ontwikkeld.
Bij Lean Management gaat het uiteindelijk om het toevoegen van waarde voor de klant door het wegnemen van verspillingen.
In dit artikel geven we je een uitleg van Lean Management met de 5 eenvoudige basisprincipes die de basis vormen van Lean. Je leest ook hoe vliegtuigfabrikant Strong door het toepassen hiervan van dieprode naar prachtig zwarte cijfers is gegaan.
Lean is een teamgerichte benadering die begint met het identificeren van klantwaarde. De waarde voor de klant zal toenemen doordat verspillingen in het proces worden weggenomen. De aanpak verschilt per situatie, maar de resultaten worden beter doordat het team zich bewust gaat bezighouden met het verbeteren van de bedrijfsprocessen.
Lean of Lean Management is een manier van kijken, denken en werken in een organisatie, die zorgt voor verbetering van de onderlinge samenwerking. Daar vloeien direct betere resultaten uit voort.
Lean Management bestaat uit 5 eenvoudige basisprincipes. Deze principes of stappen helpen de klantwaarde te verhogen en tegelijkertijd de verspillingen weg te nemen. Het spreekwoordelijke mes snijdt dus direct aan twee kanten.
Dit is de waarde voor een product of dienst vanuit het oogpunt van de eindgebruiker, de klant. Het is van belang eerst inzichtelijk te hebben wat waarde toevoegt voor de klant. Aan de hand daarvan kunnen de stappen van het proces, van klantvraag tot eindproduct, in drie categorieën worden gedeeld:
Door het proces uit te werken en de stappen te categoriseren in waardes, wordt de waardestroom inzichtelijk. Deze waardestroom loopt door de gehele organisatie, over alle afdelingen.
Veel stappen lijken waarde toe te voegen, maar zijn in werkelijkheid verspilling. Het elimineren van verspilling en reduceren van ‘Niet Waarde Toevoegende Activiteiten’ leidt tot een kortere doorlooptijd en verlaagt de kosten.
Dit is het derde principe. Het halfproduct dient door de organisatie te stromen als een flow: met zo min mogelijk verspilling stroomt je product of dienst door de organisatie. Geen wachttijden voor de volgende bewerking en zo min mogelijk verspilling. Door het verhogen van de kwaliteit van het proces en het product dalen de kosten. Dit zorgt voor een korte doorlooptijd en een verhoging van de klanttevredenheid.
Om verspilling te voorkomen is het van belang uitsluitend te produceren wat en wanneer de klant vraagt. Bij het vierde principe pull bepaalt de klantvraag de productie en niet de productie de klantvraag. Dit voorkomt overbodige voorraad en overproductie. Hierdoor blijven de kosten laag.
Bij Lean streven we altijd naar perfectie. Volledige perfectie bereik je nooit. Perfectie is wel het streven naar continu verbeteren en het weghalen van verspilling, zodat alle activiteiten in de waardestroom waarde creëren. En beginnen we weer met de cyclus bij principe 1.
Hoe een vliegtuigfabrikant met de 5 basisprincipes van Lean van rode naar zwarte cijfers is gegaan.
In de problemen
Vliegtuigfabrikant Strong is in 1923 opgericht door Andrew Strong. Het bedrijf behoorde bij één van de eerste fabrikanten die op basis van eerste testvluchten en testmodellen vliegtuigen ging bouwen. Alle onderdelen en ideeën moesten in eigen huis worden ontwikkeld en getest. De geheimhouding van de specifieke onderdelen en productie heeft een belangrijke rol gespeeld om de concurrentie voor te blijven.
Lange tijd is er sprake geweest van een bedrijfsfocus die intern gericht was. De focus heeft gelegen op productie en verkoop van de vliegtuigen en niet op de ontwikkeling en innovatie van onderdelen en modellen. Terwijl de concurrenten op zoek zijn gegaan naar nieuwe technologische ontwikkelingen en aerodynamische modellen met een betere terugverdiencapaciteit, heeft deze ontwikkeling bij vliegtuigfabrikant Strong stilgestaan.
Het bedrijf kwam te kampen met grote problemen. De kwaliteit was ronduit slecht, klanten waren ontevreden, het onderhanden werk was ‘sky high’ en het resultaat onderaan de streep was dieprood.
John Strong, huidige directeur en kleinzoon van de oprichter, zat met zijn handen in het haar. Hij trok adviseur Henry Hope, met als bijnaam Mr. Lean, aan om hem te helpen uit deze problemen te komen.
Waarde bepalen
De eerste stap waar ze naar gingen kijken, waren de kwaliteitsproblemen. Want als één ding helder is, dan is het dat vliegtuigmaatschappijen met betrouwbare vliegtuigen willen werken. Hiermee zorgen ze ervoor dat ze veilig, op tijd en met zo min mogelijk kosten hun passagiers en goederen kunnen vervoeren. Daarin zit de waarde voor de klanten van de vliegtuigfabriek.
Waardestroom in kaart gebracht
Vervolgens gingen de heren Hope en Strong met de teams kijken hoe de processen in de fabriek lopen: vanaf de klantorder tot en met de levering. Na de analyse met alle betrokkenen van deze waardestroom bleek dat de processen niet goed op elkaar waren afgestemd. Dat leverde veel onderhanden werk op omdat de verkeerde onderdelen op de verkeerde momenten gemaakt werden. ‘We moeten wachten op onze spullen’, was dan ook een veelgehoorde klacht van de mensen van de productie.
Conclusie: geen flow
De korte en bondige conclusie was dan ook: de waardestroom stroomt niet en het ontbreekt aan flow. Daarbij was de informatie en planning ook zo ingericht dat je niet kon spreken van pull - de klant moet aan het proces trekken. En niet alleen de klant neemt het vliegtuig af, maar ook de interne klant: de collega die het onderdeel nodig heeft.
De rondgang door de fabriek en het bekijken van de processen leverde veel inzichten op. Er kwam een grote bewustwording van wat waarde is voor de klant en wat dat tegenwerkt. De vijand van waarde is ‘verspilling’ en die proberen we met Lean tegen te gaan.
De oplossing
‘Hoe gaan we dit oplossen?’ vroeg John Strong zich af. Henry Hope organiseerde een simulatiespel voor de productie van een miniatuurvliegtuig waardoor heel snel duidelijk werd welke stappen er genomen moesten worden:
Samenvattend: continu verbeteren en streven naar perfectie. Bij Lean gaat het erom dat iedereen in de organisatie zich bewust is dat het altijd beter kan en ook weet en in staat is om de verbetering te realiseren. Dit is geen doorgeschoten perfectionisme, maar een nuchtere houding en streven naar beter.
Eindresultaat: zwarte cijfers
En hoe liep het af voor de vliegtuigfabrikant? Een jaar later waren de cijfers van dieprood naar prachtig zwart gegaan. De kwaliteitsproblemen waren tot een fractie teruggebracht van wat het was. Als je door de fabriek liep, was er orde, overzicht en zag je tevreden medewerkers rondlopen.
Enthousiast geworden van deze basisprincipes en hoe Strong naar zwarte cijfers is gegaan? Benader ons om in jouw organisatie de processen te optimaliseren of schrijf je in voor het Bunt Lean Simulatiespel. Tijdens deze training gaan we op een praktische manier met de 5 basisprincipes aan de slag aan de hand van een simulatietool. Tijdens deze dag wordt de stap gemaakt naar de eigen praktijksituatie om de aangeleerde principes direct toe te passen in de praktijk.
Verbeter je bedrijfsresultaat, ga aan de slag met Lean en schrijf je hier direct in!
Jan Sterk, Directeur en Leanexpert